Road Tested and In Serial Production: Pentatonic Battery Enclosures
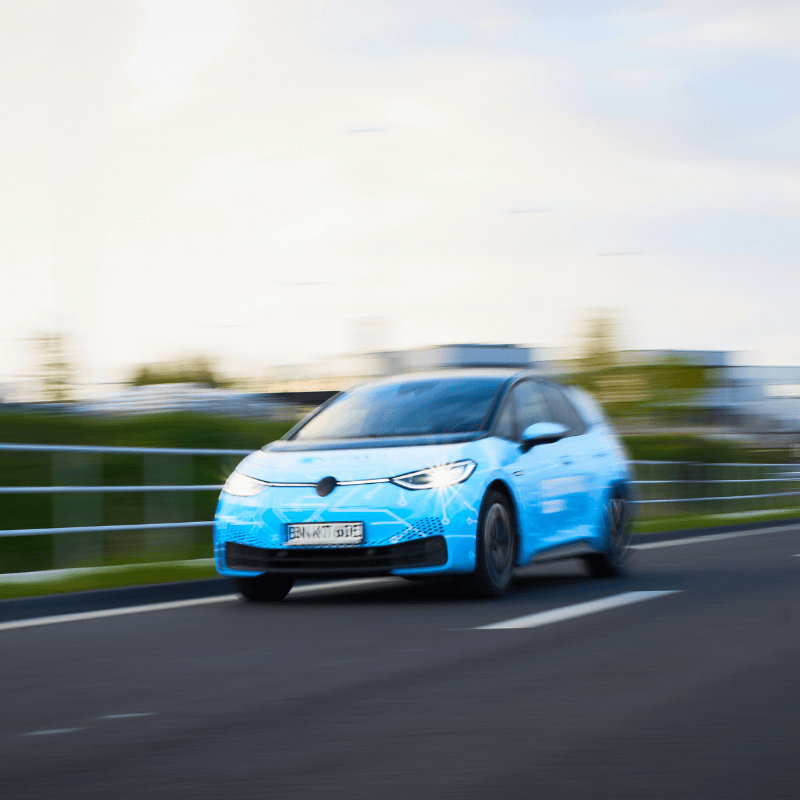
Road Tested
Between 2021 and 2023, we expanded our innovation footprint by acquiring one hybrid and two full battery electric vehicles (BEVs), each retrofitted with our Pentatonic Battery Enclosures. These vehicles have been rigorously tested across diverse global environments—spanning climates, terrains, and road conditions—to validate the performance and durability of our technology. Since then, our Pentatonic Underbody Skid Plate has successfully entered serial production, and we’ve secured a new order for full-BEV lower housing units. Collectively, the fleet has logged over 100,000 miles, and we continue to gather live data from real-world driving to inform future development and accelerate our path toward next-generation mobility solutions.
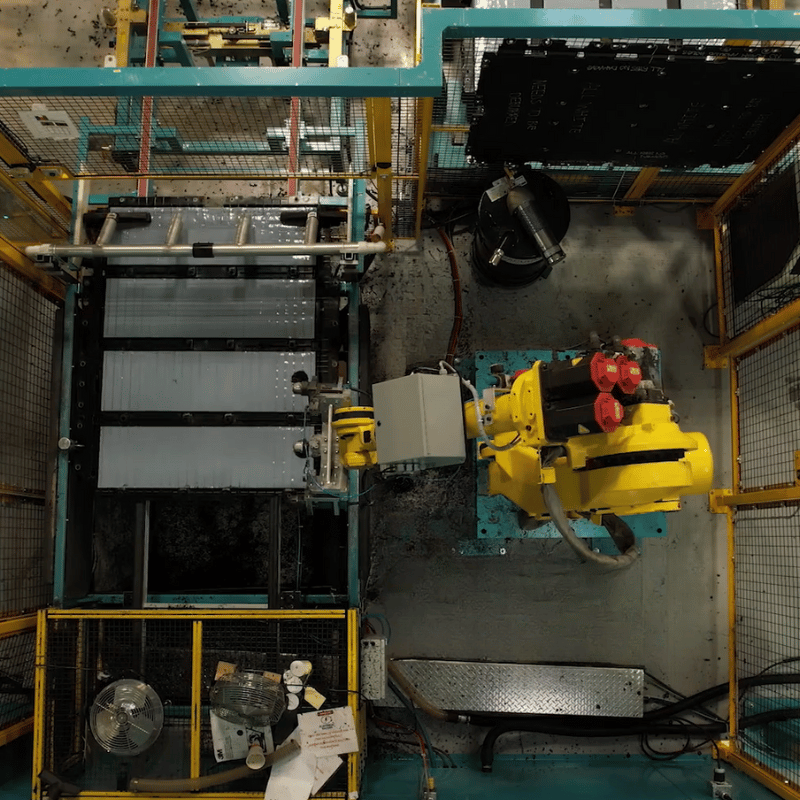
In Serial Production
Our advanced underbody protection skid plate has officially entered serial production, offering a high-performance solution engineered for efficiency and reliability. Built on a fully automated compression molding process, the manufacturing line features:
- Industrial mobile robots for seamless material handling
- A closed-loop process ensuring consistent quality and minimal waste
- Complete process simulation for predictive performance and design validation
- Real-time data monitoring for full traceability and production transparency
For our customers, this means:
- Accelerated time-to-market with a robust and scalable production setup
- Enhanced product consistency and reduced variability across builds
- Improved sustainability through optimized material usage and energy efficiency
- Streamlined integration into existing vehicle platforms with validated performance data
This next-generation skid plate delivers not only superior protection but also manufacturing intelligence that aligns with our customers' goals for innovation, quality, and operational excellence.
Benefits
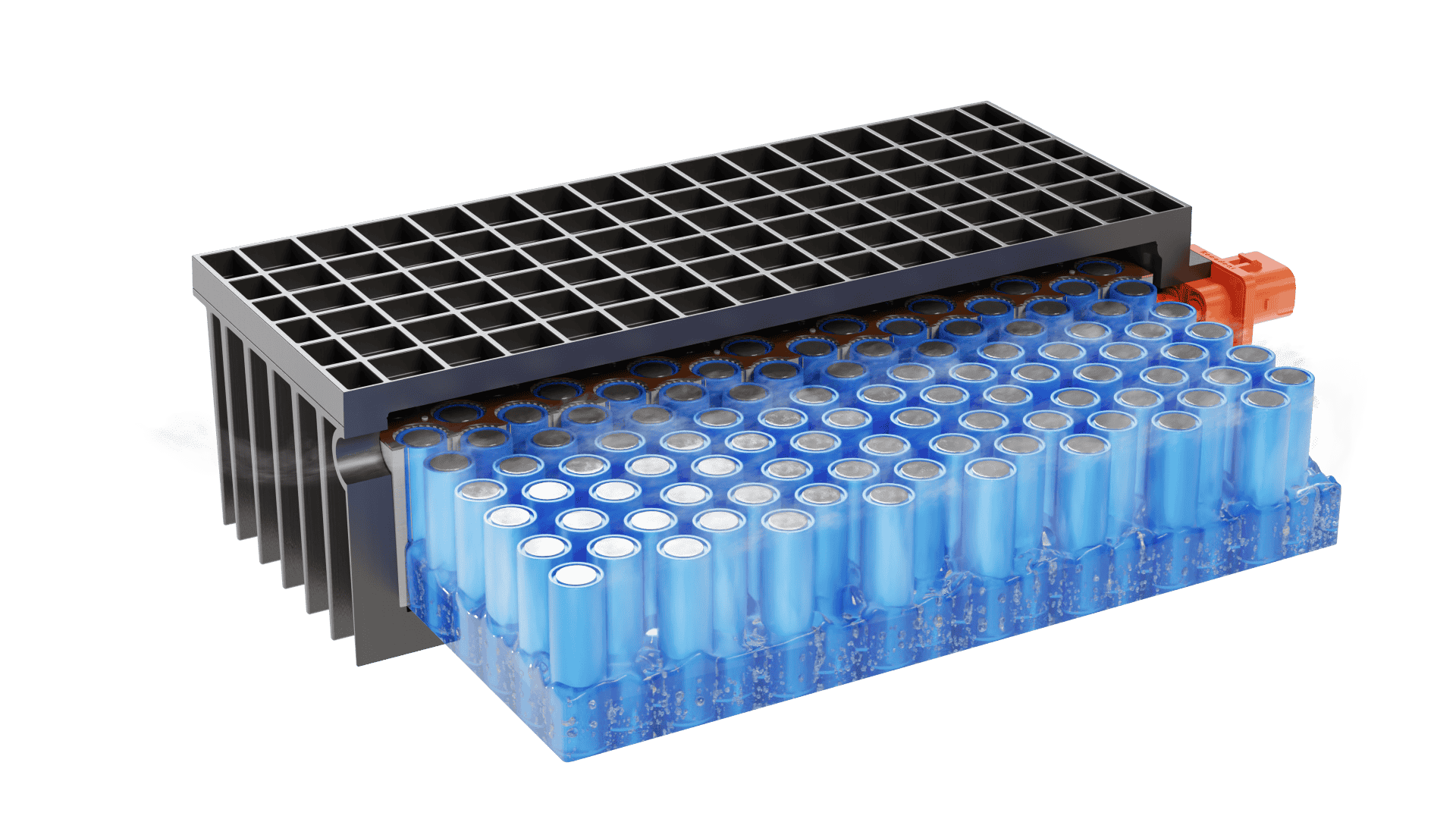
Thermal Systems
From water-glycol based cold plates to full plastic design and novel heat transfer fluids, we have the thermal management solutions our customers need.
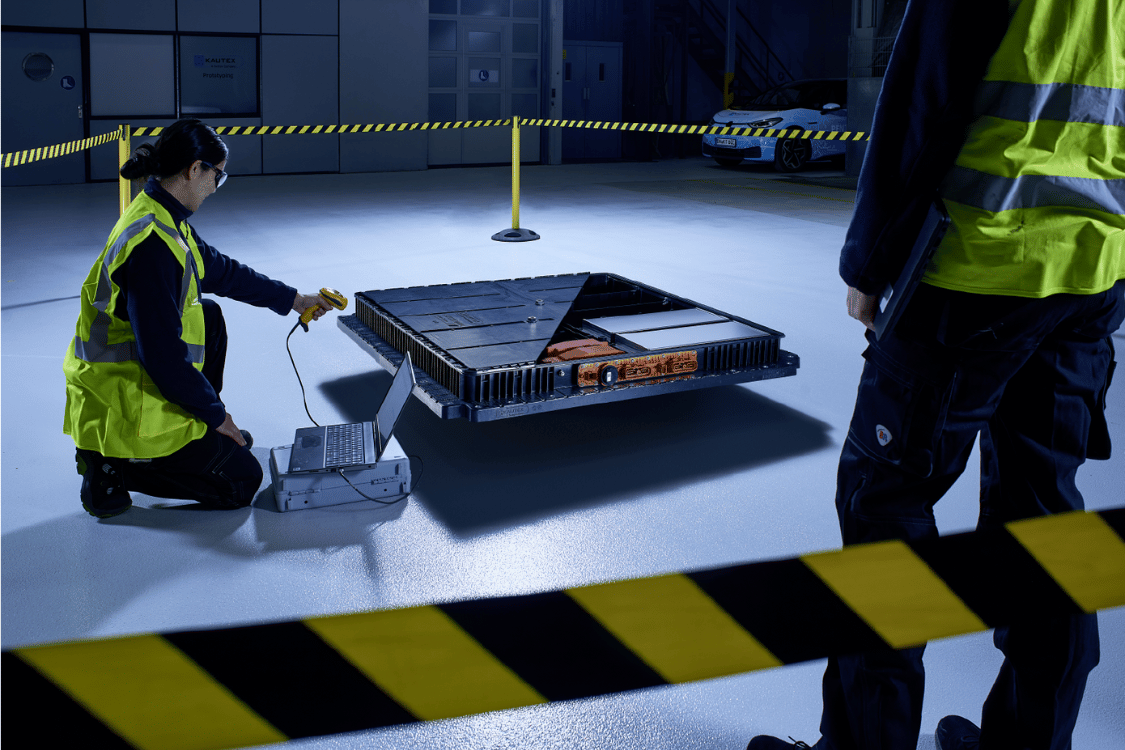
Safety
The materials and processes we use make safety the highest priority when it comes to production and application. Our non-conductive housing material reduces risk of electrical shock and corrosion, unlike our steel and aluminum counterparts.
Feature Integration
Features and thermal management components like cooling plates are integrated into one fully capable, lightweight system. Reduction of secondary process steps simplifies the assembly process, reducing the customer bill of material and improving cost by up to 20 percent. Fewer assembly steps reduce the number of sealing joints, which lessens the risk of leakage.
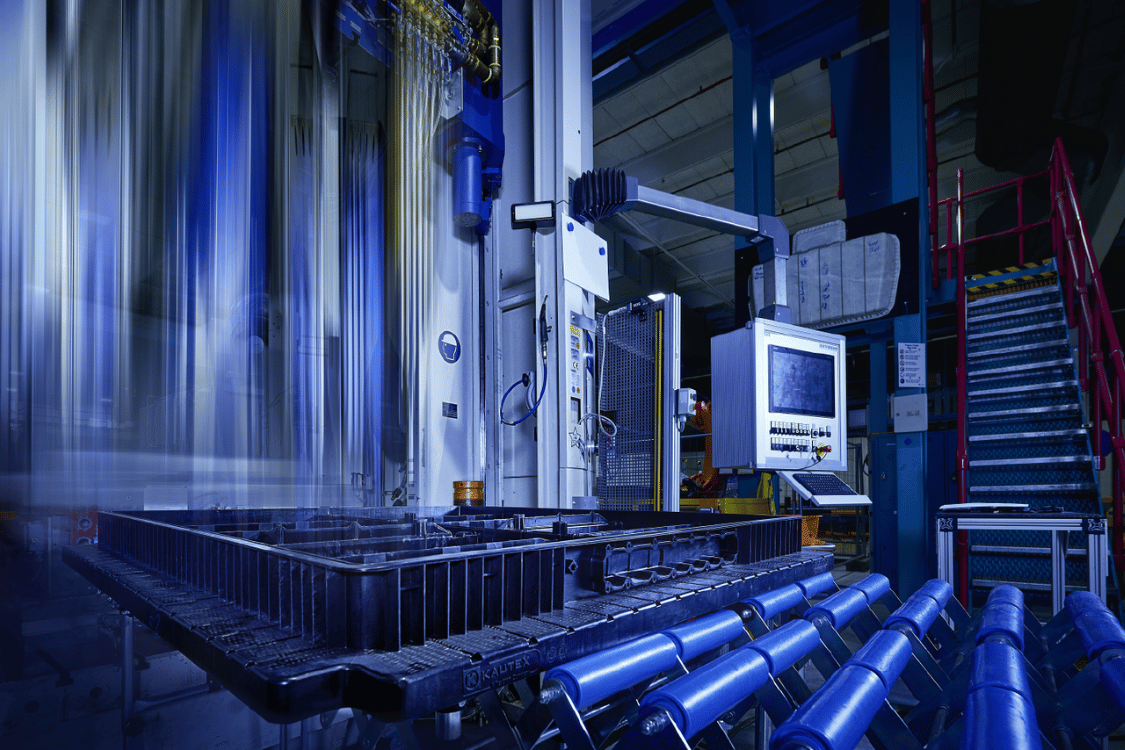
Manufacturing Process
Our "one shot" process uses reinforced materials and integrates structural elements directly into the injection or compression molding process, eliminating timely assembly steps at the customer's facility.
Benefits include fewer secondary operations, such as welding and riveting, shorter cycle times than steel and aluminum counterparts, and improved leak-tightness.
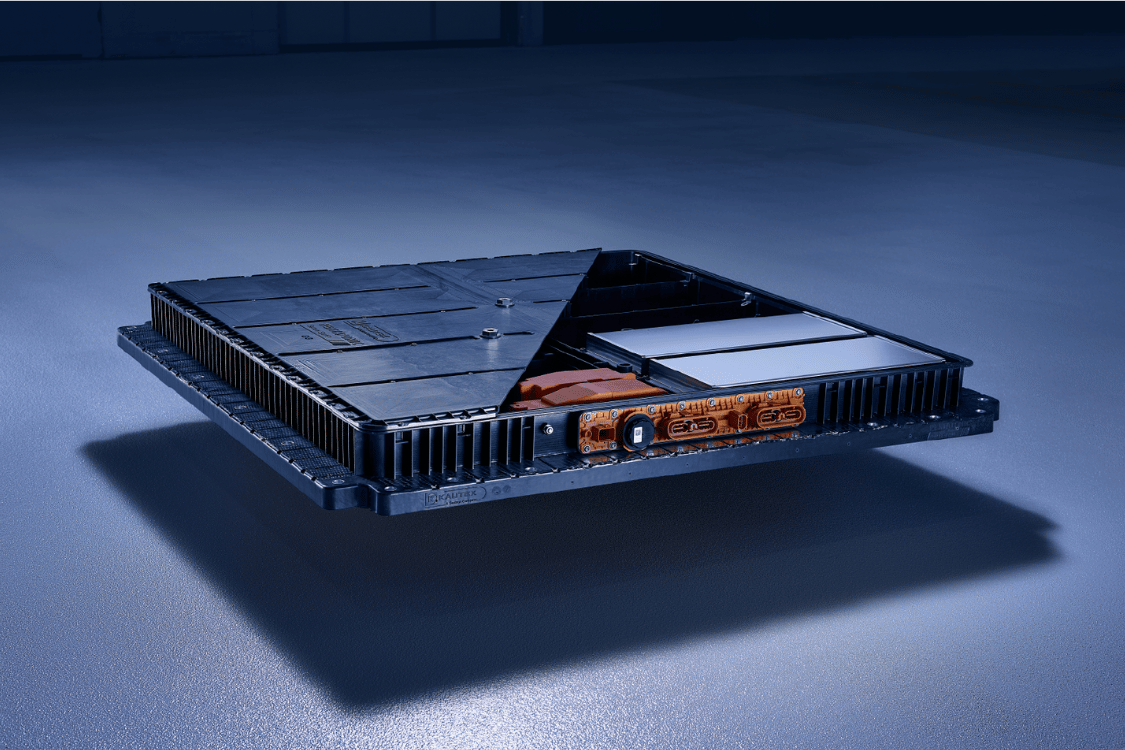
Weight
Pentatonic weighs up to 30% less than its steel and aluminum counterparts, which improves the range of the vehicle and allows the opportunity to adjust chassis components – such as suspension and brake systems.
Pentatonic allows the opportunity for maximum payload capacity while limiting CO2 emissions as well as energy consumption in both the vehicle and within the supply chain.
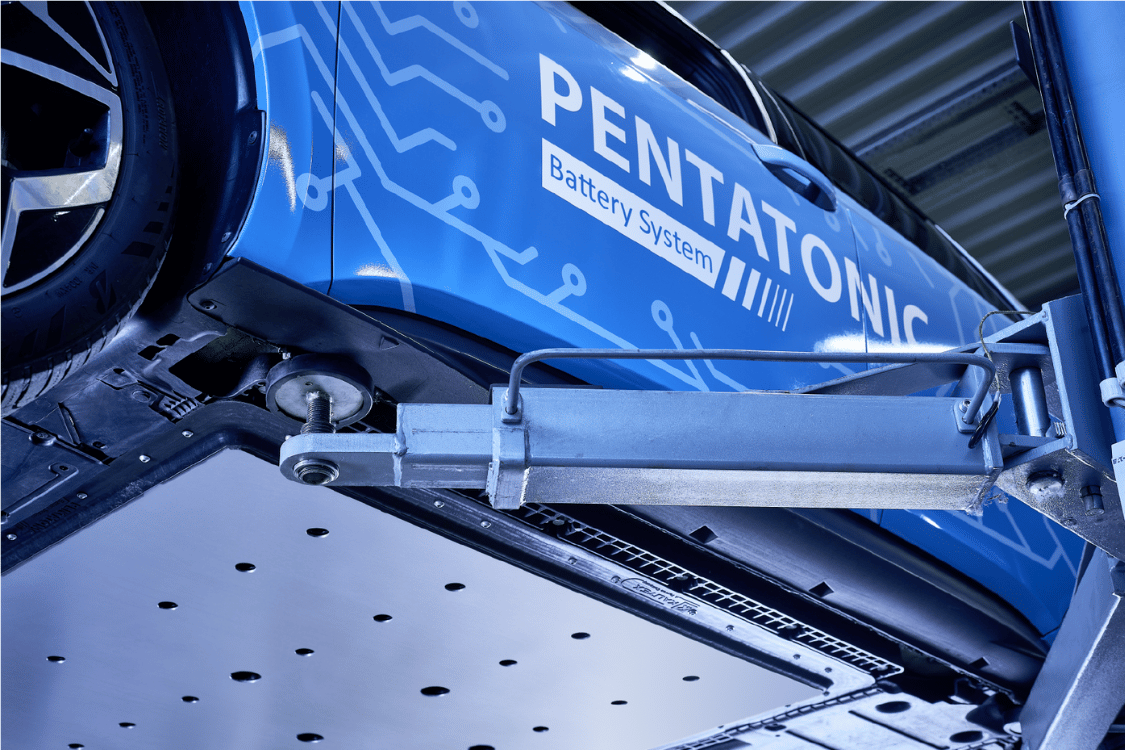
Volumetric Advantages
The Pentatonic Battery Enclosures require less clearance between the housing and the modules due to the isolating characteristics of our materials and the increased integration (e.g cooling plates) during the production process.
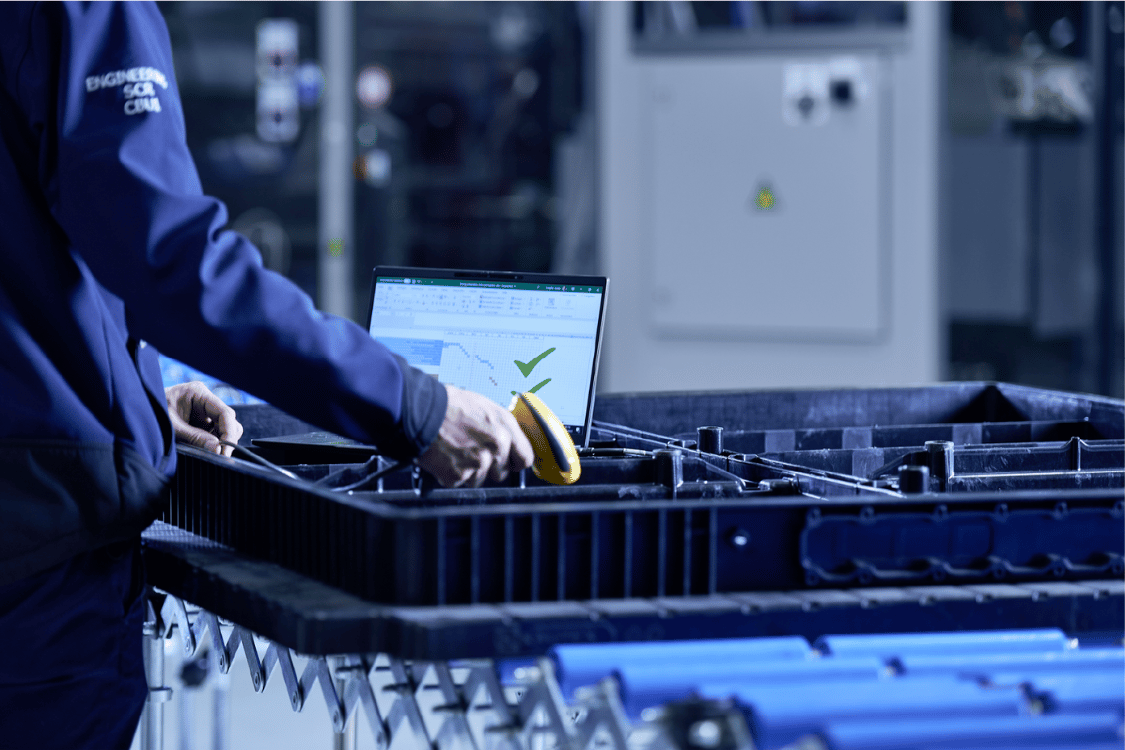
Homologation
As the pioneers in plastic fuel tank production, our decades of expertise with fire tests, leak tightness proofing, and crash tests are utilized and extended to the requirements in designing as well as producing composite battery systems, such as ECE R100 or GB38031-2020.